ADVANCING RENEWABLE SOLUTIONS
FOR A SUSTAINABLE FUTURE
AN INSIDE LOOK: THE B³: BIOENERGY, BIOREFINING, AND BIOMATERIALS TEAM
Overview
What do corn stover, switchgrass, and wood chips have in common? These materials are all considered types lignocellulosic biomass. Biomass is the largest single source of renewable energy in the world, representing 3.9 quadrillion of 9.6 quadrillion British thermal units (Btu) in 2015 (EIA 2016). Biomass includes agricultural waste products, forestry waste products, municipal green waste, and algae. We estimate that, in the US, up to 1 billion tons of biomass waste could be made available each year for the production of renewable energy, liquid fuels, chemicals and materials. Furthermore, biomass only represents the non-edible portion of plant waste so its usage does that negatively impact the agricultural and farming sectors that are in charge of providing our food supply. CE-CERT’s Biomass Fuels & Co-Products lab has dedicated over a decade of research to advancing biomass conversion. We are focused on understanding the fundamentals of how biomass can be broken down by chemical and biological processes as well as developing radically efficient technologies to convert biomass into liquid fuels and chemicals. Finally, we are also focused in developing new biomaterials, such as high-performance fibers and resins, that can replace conventional plastics and wood pulp products that are manufactured non-sustainably and cause environmental damage.
CE-CERT is Leading the Way for Research in Environmental Studies
2023 Research Highlights
Through project funding from the US Environmental Protection Agency, we have developed techniques for transforming newly legalized industrial hemp into a high-performance “hempcrete 2.0”. With our team of graduate and undergraduate students, we developed a stronger and more insulating hempcrete that can be mass-produced at a lower cost than previous traditional hempcrete products. We apply CELF (co-solvent enhanced lignocellulosic fractionation) pulping of raw hemp sticks (no decortication) directly to achieve the material properties we desire before incorporation into hempcrete. Furthermore, we have found that this technique is also fully compatible with other hardy biomass feedstocks such as almond tree waste and elephant grass.
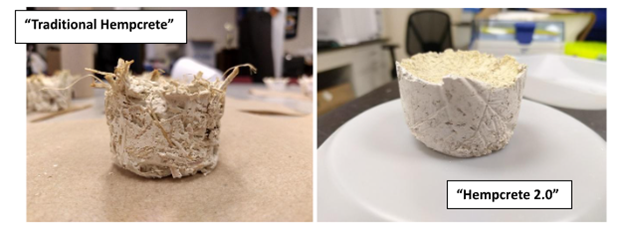
Through project funding from the US Department of Energy, we have partnered with researchers at Oak Ridge National Laboratories (ORNL), National Renewable Energy Laboratories (NREL), and University of Tennessee Knoxville (UTK) to develop a high-fidelity computer model that calculates the economics and environmental impacts of a full-scale biomass biorefinery utilizing CELF technology that transforms poplar wood and corn stover into sustainable aviation fuels (SAFs), green chemicals, and fuel alcohols. The analysis demonstrated the possibility of supplying alcohol-derived SAF to the market at competitive prices – as low as $3.15/GGE (gallon of gasoline equivalent) – as well as carboxylic acids and esters. This manuscript was recently accepted into the prestigious journal of Energy & Environmental Science.
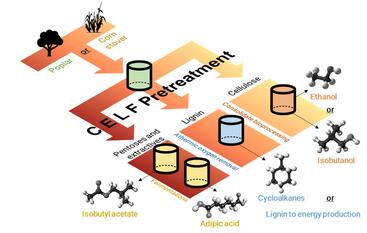
Through project funding from the Advanced Research Projects Agency-Energy (ARPA-e), we are currently investigating the manufacture of lignin-based polyurethanes (LPU). Specifically, this ambitious project seeks to develop lignin-polyurethane insulating foams for home and commercial installation while achieving greater sustainability and the elimination of toxic ingredients in traditional polyurethane manufacturing. In 2023, our team has not only achieved all the performance metrics (strength and insulation) for our LPU products, but we have also developed an LPU process that completely eliminates the use of toxic isocyanates in a new formulation called non-isocyanate polyurethane (NIPU).
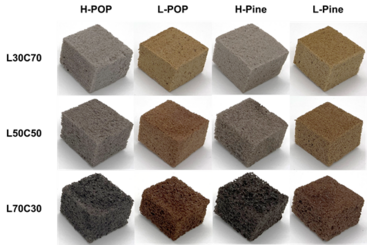